Projects: Parker Fly 12-string
Parker Fly 12-string Modification
The goal of this project was to convert a six-string Parker Fly electric guitar into a 12-string electric guitar. The scope of work included CAD/CAM design and fabrication of new parts, a variety of tests and calculations, and modifications and installations to an existing Parker Fly electric guitar. With the exception of the additional six tuner holes drilled into the headstock and the replacement of the stock nut with a nut slotted for 12 strings, all modifications made to this guitar, described herein, are reversible. This project was completed through the Electric Guitar Innovation Lab at WPI (EGIL) over the course of one 7-week term in spring 2018 and intermittent work in summer and fall 2018 with the majority of time spent developing a solid plan of action.
Project Background
The Director and PI of EGIL, V.J. Manzo, who also served as this project's sponsor, primarily plays Parker Fly model guitars and wanted a 12-string electric guitar with the unique qualities of a Parker Fly guitar: thin, lightweight instruments wrapped in a carbon fiber exoskeleton that have exceptional resonance and sustain. Parker Guitars never produced a 12-string Fly model (or any other 12-string model) and, in 2015, ceased production of Fly guitars altogether. Our team explored a variety of approaches toward converting an existing Parker Fly guitar into a 12-string electric guitar. This report summarizes the major milestones of this project.
Tension
We needed to understand the maximum amount of string tension a Parker Fly could handle. Parker Fly guitars most commonly have a floating bridge with a unique flat spring rated for specific string tensions; Flys ship with a set of 9-gauge strings and a “9 spring” installed as well as an additional “10 spring”; additional tension springs up to a “12 spring” could be ordered directly from Parker Guitars. Knowing this allowed us to assume that the Fly could, at least, support the tension of a set of 12-gauge strings.
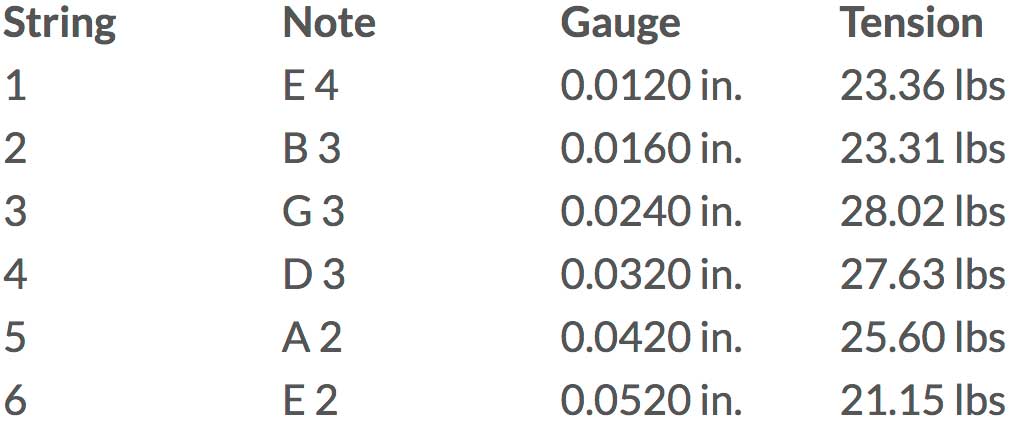
With a 12-string set of strings, the guitar (truss rod, bridge, etc.) would need to support about 250 lbs. of tension in total resulting from a set of 10-gauge 12-strings as follows:
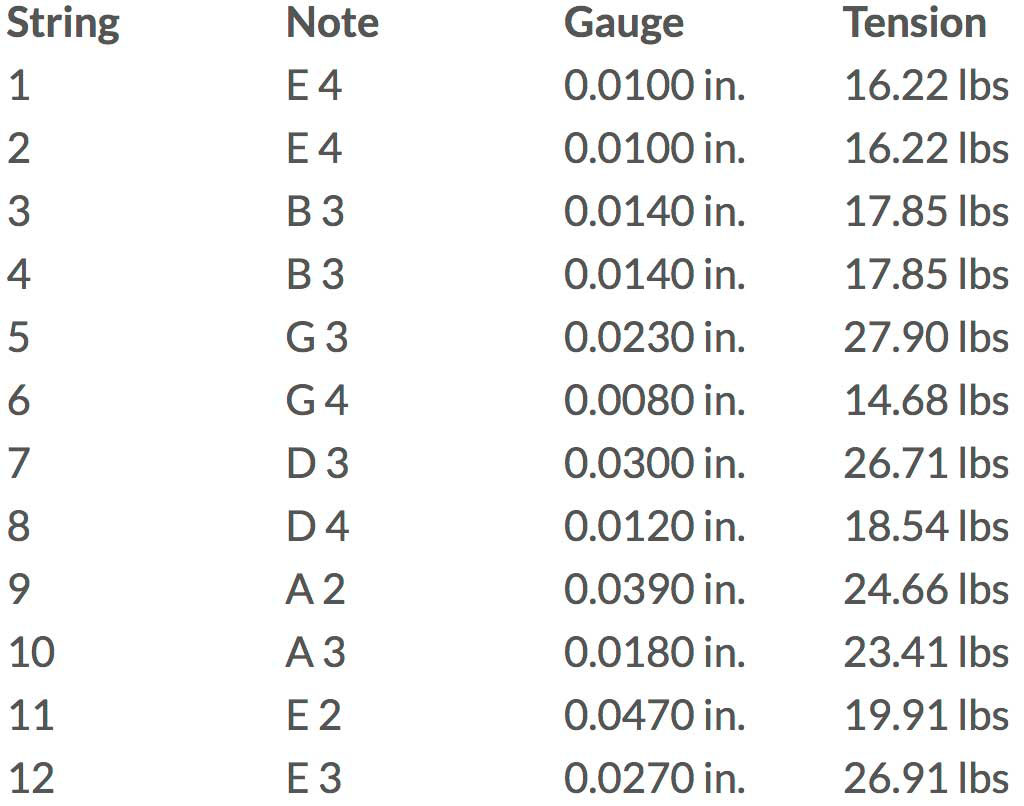
The carbon fiber exoskeleton around the guitar neck should theoretically add enough strength to ensure that the neck does not simply snap from the additional tension. Our main concern with the added string tension was wood compression at the truss rod anchor.
Wood Types
The Parker Fly came in several models that primarily differed from eachother in the woods used for the body and, in a few models, the neck. The Fly Deluxe, Classic, Supreme, Artist, and Concert, for example, have necks made of basswood; the Fly Mojo model has a mahogany neck. Mahogany is a stronger wood than basswood, so, we considered neck wood as a potential factor in selecting the right Fly model to use for this 12-string modification. We performed stress test simulations on both basswood and mahogany in order to determine the safe zones for tension before the wood begins to compress.
Through our tests, we determined that, in principle, both basswood and mahogany Fly necks are well within the safe-zones to support the added string tension without causing wood compression.
We ultimately chose a 2011 Fly Mojo for this project. This late-era Fly differed from earlier Flys in that it had a centered dual-action truss rod placement whereas Parker Fly guitars from previous years had a side-positioned truss system.
The Bridge
We needed to design a new bridge to accommodate 12 string saddles. The floating bridge of most Parker Fly models is capable of switching between two distinct modes of operation: a floating mode in which the bridge is capable of bending forward or backward (down or up in pitch, respectively) with the use of a whammy bar, and a fixed mode in which the bridge locks in position and is only capable of bending forward. A permanently fixed, or "hardtail", bridge was available standard on fewer Fly models and did not come standard on the Fly Mojo.
We modeled both Fly bridges (floating and hardtail) in CAD/CAM and ultimately chose to adapt the more common switchable floating/fixed bridge. The new bridge we designed was made to fit as a drop-in replacement for the stock Fly bridge with no additional modification to the instrument body needed.
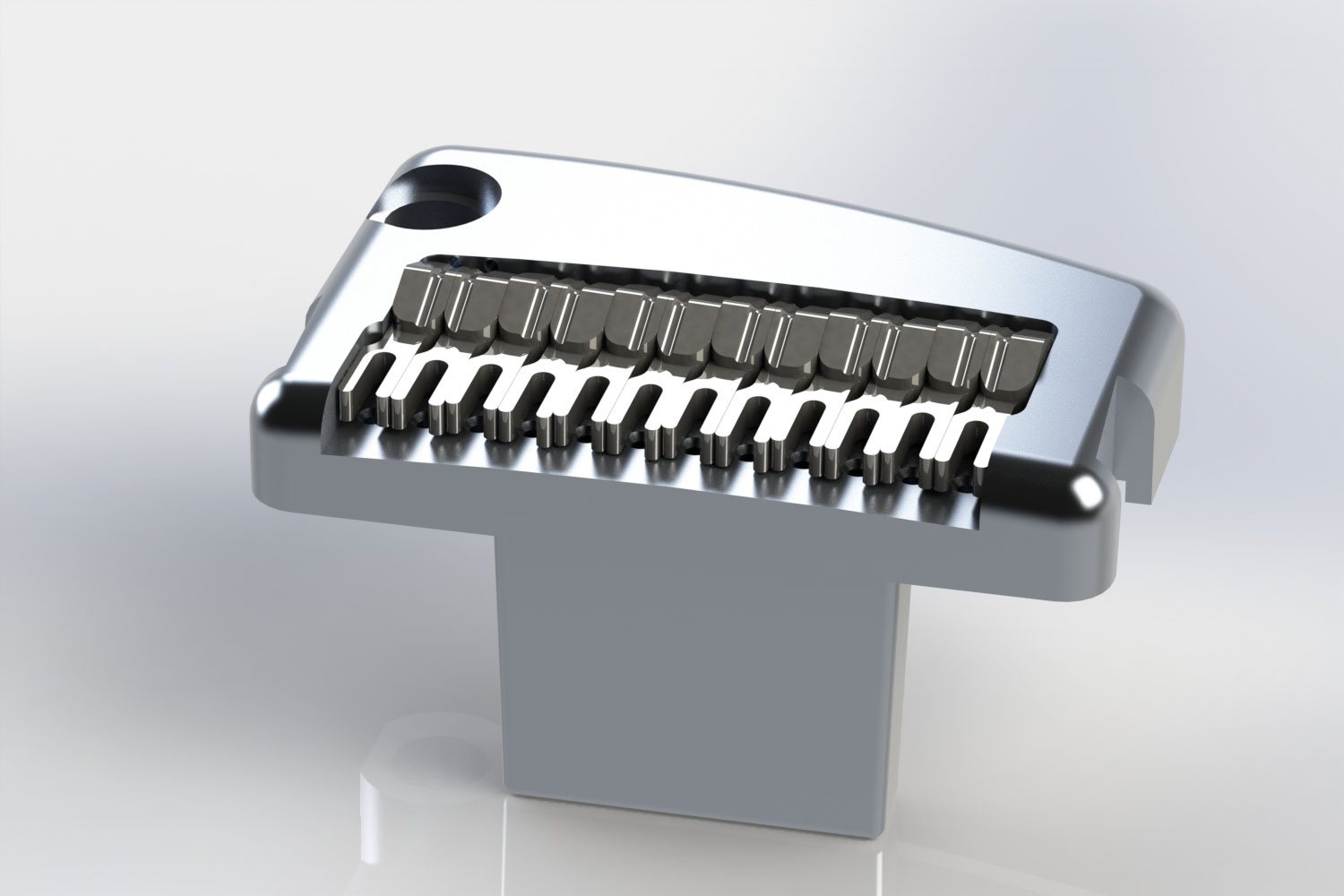
Early 3D model of our 12-string Fly bridge adaptation prototype
The bridge prototype design was further refined, and, eventually, fabricated from aluminum, the same material as the stock bridge, according to our density tests.
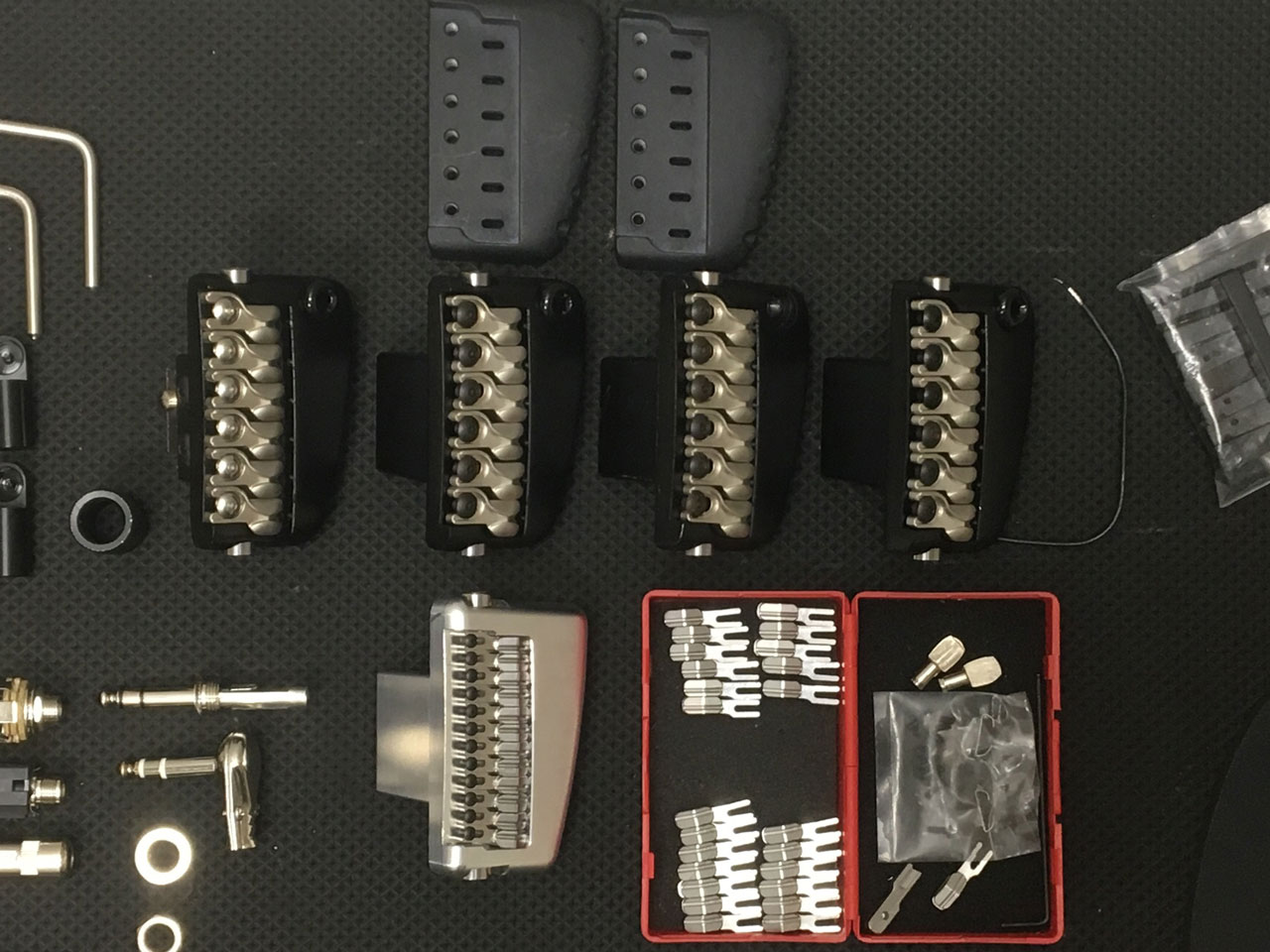
The Saddles
The saddles used on the Fly were nearly identical among Fly models. They were adjustable using a setscrew in the bridge and had piezo elements fixed underneath that ran into a summing board inside the body cavity and then run into a preamp also located the inside of guitar.
We developed a tool to calculate the appropriate string spacing for 12 string pairs (six courses) in the space of six strings.
Note: in order to allow you to use the spreadsheet, but not overwrite it, this link will open a Google doc, which will prompt you to copy the file to your own Google Drive
We modeled the stock saddles in CAD and designed slimmer “left and right” pairs of saddles in CAD/CAM capable of being adjusted within the new bridge.
The Bridge Block
In order to improve tuning stability, we developed a Fly “bridge block” to replace the tension spring; this effectively turned our floating/fixed bridge into a reinforced fixed-only bridge.
We cut a steel rod and utilized the existing tension wheel to secure the block in place.
The Tuners
We needed to fit six additional tuners somewhere on the Fly headstock, which is quite thin. We considered a variety of approaches including setting the additional tuners through the top of the headstock with the posts buried into the wood , where the tuner string-hole would be accessible from small holes in the headstock.
In order to identify the maximum number of viable options for fitting the additional tuners on the headstock, we modeled the Fly headstock and the Sperzel short-post locking tuners used on the Fly in CAD.
Models of Fly headstock and Sperzel tuners
After modeling, we fabricated several “practice pieces” of mahogany in the shape of the Fly headstock out of wood and acrylic. We used these pieces to test fitting tuning pegs in place in various configurations using Sperzel short-post and long-post tuners. Fitting the tuners was not the only concern: we needed to avoid string collisions at the nut, which required us to consider string gauges as well. We ultimately decided on an alignment configuration that utilized a single-piece mounting plate made from laser-cut aluminum; the plate was devised as a means to help secure the tuners in place by anchoring them to eachother. Having explored a variety of options for tuning peg alignment and orientation on the headstock , we ultimately concluded that a 7 over 5 placement of short-post and long-post tuners was ideal. We also replaced the stock Sperzel tuners, which had square tuning knob buttons, with Sperzel locking tuners with knurled knob buttons , which was more about aesthetics than necessity.
The Nut
The guitar nut was replaced with a blank “new old stock” original Parker Fly nut purchased online . The actual nut used in Fly production, however, changed somewhere around the year 2010 to a nut that more closely resembles a Gibson-style nut. Our friend Eddie Hulse, luthier at Hulse Guitars , removed the existing painted-in nut, sanded the blank Fly nut to the shape of the existing nut, fit the nut into the headstock, and carved new slots in the nut using the same tool we created to calculate string spacing.
Strings
The original intention for this project was to modify a Parker Fly Concert guitar, which has a spruce body and a basswood neck. The Fly Concert has an under-saddle piezo system and no magnetic pickups; in this regard, phosphor bronze strings (as opposed to nickel strings) help emphasize the “acoustic guitar” sound through the piezo output. We used a D’Addario EJ38 12-string set for our prototyping and during our initial tests.
When we decided to use a Fly Mojo for this modification, we naturally opted to take advantage of the magnetic pickups. We used D’Addario EXL150 12-strings.
The Piezo Elements and Magnetic Pickups
We affixed a 3 x 0.4mm ceramic piezo disc under each of our saddles, and wired the piezo elements of each lower string in each course and the higher string in each course to separate summing boards. Both summing boards were then wired into one Fishman Powerchip preamp.
We wired the piezo elements in this manner so that we can, in the future, explore the notion of having separate volume knobs for each set of six strings toward the idea of controlling the piezo output level of the upper strings; allowing the guitar to go from a “six string” to a “12-string” by adjusting a volume knob. The issues of piezo bleed will be explored toward this end on a periodic but continual basis.
The Fly Mojo model came stock with a Seymour Duncan Jazz pickup in the neck position and a Seymour Duncan JB pickup in the bridge position.
While the JB is a good pickup for most applications, we decided to experiment with replacing it with the bridge version of the Seymour Duncan Jazz pickup, effectively giving this 12-string a set of SD Jazz pickups. We ordered the “trembucker”-spaced version of the SD Jazz bridge pickup through the Seymour Duncan Custom Shop Floor.
Final Result
The final result is a truly unique 12-string modification to an already unique electric guitar.
Considerations
This guitar sounds great as it is. It has all of the same comfort and playablity of a thin-neck, lightweight Parker Fly with a very distinctive 12-string timbre. While this project was a success, there are, however, a number of new areas of exploration and experimentation that have emerged as a result of this effort. The following considerations were noted during this project and will continue to be explored by our lab on an ongoing basis both with this 12-string Fly model and future replications of this mod.
String Arrangement
The Rickenbacker string arrangement is where the lower string in each string course is on the bottom and, thus, strummed first when strumming downward. This arrangement has a subtle but different sound from the traditional 12-string string arrangement where the higher string is strummed first on downstrokes. Our bridge can accommodate either string arrangement; but needed to file a new nut to accommodate this arrangement. Having compared both string arrangements, the PI prefers the traditional 12-string string arrangement over the Rickenbacker string arrangement for this instrument because the upper voice is more prominent with downstrokes with normal strumming.
Additional Tuning Peg Holes
Four of the new holes we drilled are very close to edge of the headstock. The pegs are firmly fixed into the headstock, but this creates somewhat of a cosmetic issue. We were successful in not breaking the outer plane, but, in the case of four points, there is mostly just carbon fiber which, now, no longer has a wood backing.
We considered using smaller tuners like the very lightweight Gotoh ST31 Stealth-key tuners, but wanted to retain the original Fly tuner qualities as much as possible. The additional six Sperzel tuners do not add a significant amount of weight to the headstock.
The Bridge
Apart from planning and running simulations, fabricating the bridge was the most time-consuming part of this process. The shape is very unique and the process overall presents many opportunities to make simple mistakes that require a restart. Cutting string holes in the bridge is much more difficult than cutting holes in the headstock. The bridge is a smooth-feeling aluminum, but we may powder coat the bridge in black at a later date or in future replications of this project.
String Gauge
Toward the objective of experimenting with the balance of "upper strings" and "lower strings" in each course of this 12-string, the string gauge may have a greater impact on the overall tone than pickup adjustement/replacement. In particular, increasing the string gauge of the “upper-octave” strings. The first nickel-wound set we used for this instrument was the D’Addario EXL150; this seems to be the most widely used set used for electric 12-strings. The relative string sizes in each course of this set appear to be modeled closely after the courses used on acoustic 12-string guitars.
Electric 12-strings, obviously, rely on magnetic pickup for their sound in a way that is fundamentally different from their acoustic 12-string counterparts. We will continue to examine and experiment with the string gauges of the upper-octave strings toward altering, if at all, the relative balance both strings in each course of this instrument. While it’s not difficult for us to file the nut slots to accommodate for increased string gauges, we will need to carefully calculate for any added tension. String balance within courses on electric 12-strings presents an area of exploration that we will continue to examine.
Tolerances
It is worth noting that the original Parker Fly floating bridge, saddles, and other components that were designed by Ken Parker and used in the earliest production of Flys beginning in the 1990s had subtle but significant differences from the Parker Fly Mojo from 2011 that we used in this project. Though some aspects of the Fly manufacturing processes were automated, there are also very subtle differences among instruments in the same model simply by virtue of machining tolerances and hand-work.
For instance, the string holes in the stock Fly bridge of this instrument didn't align 100% with the top point of contact of the saddles. The string holes of our first bridge prototype didn't align 100% either, so we modified our saddle pieces and our bridge holes to both accommodate larger strings and align the holes better with the saddle notches only to discover that some of the stock Fly bridges we examined also didn't align as expected. These tolerance differences didn't seem to have any noticeable impact on playability of the instrument, but are worth noting.
As an example of how these tolerances impacted our work on this 2011 Fly Mojo, in addition to fabricating the aluminum front-plate we put over the front of the headstock, we also fabricated a mirrored backplate that would fit the backside of the headstock. The plates are the same shape and size, but, surprisingly, both sides of headstock are not. These subtle variations require that some degree of assessment be conducted prior to replicating this mod on future Flys.
Other Things
In future iterations and potentially for this instrument, we will powder coat the bridge; the aluminum is smooth to the touch, but powder coating is an easy process and adds a finished look. We also created a version of the aluminum headstock frontplate that has the Parker Guitars logo etched into it, which we have not requested permission from Parker Guitars to picture.
Project Personnel
V.J. Manzo, Founding Director and PI of the Electric Guitar Innovation Lab; project sponsor
Ryan McKenna, WPI alumnus and Research Associate for the Electric Guitar Innovation Lab; electronics integration
Brent Reissman, WPI undergraduate student and EGIL student researcher; bridge modification, tuner, nut, and headstock modeling, simulation, and mockup design, headstock plate modeling and fabrication, headstock hole-drilling, and tuner, headstock plate, and bridge installation
Alan Hunt, WPI undergraduate student; bridge and saddle modeling and fabrication
Colin Mashack, WPI undergraduate student; bridge and saddle modeling and fabrication
Nathan Rose, WPI undergraduate student; tension calculations and string spacing calculations
Tom Ward, WPI undergraduate student; wood tension calculations and simulations and string spacing calculations
Special thanks to:
Ken Parker for a variety of insights into the original Parker Fly bridge and piezo elements
Billy Campbell and the many great people in the Parker Guitars forum for the thoughts and encouragement throughout this project
Eddie and Andy Hulse of Hulse Guitars for the final setup of the instrument